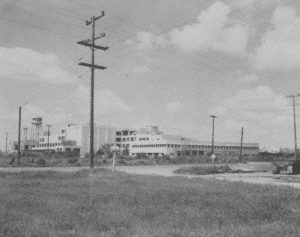
In 2014, I walked into the old Campbell’s Soup plant in south Sacramento with a camera, clipboard, a pad of paper, a limited asset list, and noted appraiser Bob Podwalny. Our assignment was a retrospective 2013 property tax appraisal.
Comstock’s article about the facility’s redevelopment references the plant as one of the “oldest and most historical … sites that helped give the city its Sacratomato nickname.” In the appraisal profession, we often refer to old and historical facilities as “legacy” in the sense that they’ve been superseded but are difficult to replace. I wrote about another legacy food processing appraisal here.
To take Leo Tolstoy a little out of context, each legacy facility is old-fashioned in its own way. Accordingly, the Campbell’s Soup facility presented a number of interesting legacy appraisal challenges.
The facility is huge. While not as big as the USS-UPI Steel facility in Pittsburg CA I appraised later that decade – USS Steel is the largest industrial facility in California – the Campbell facility, on 129 acres, included over 1.6 million square feet under roof: 84,000 square feet of office space, over 630,000 square feet of warehouse space, 34,000 square feet of cold storage space, and over 863,000 square feet of production and other areas. The site included an extensive compressed air system, onsite boilers, an impressive solar power array, and complete water and sewer treatment system, as well as plant wide cooling, HVAC and electrical infrastructure.
For valuation purposes, the equipment fell into two categories: production equipment included all of the processing of food products from initial cleaning and preparation through blending, canning, cooking, labeling, packaging and palletizing; support equipment included material handling and various utilities as well as equipment used for mechanical and administrative support. Most equipment could be valued using the sales comparison approach; the plant-wide can-conveying system and a few pieces of propriety equipment were appraised with the cost approach.
That limited asset list? While most equipment was listed, important details were missing. Our first challenge was a thorough inspection of all the equipment within the facility to collect or verify verified make, model, serial number, capacity, condition and other related information. With equipment and infrastructure packed into 1.6 million square feet, this was a time-consuming undertaking. Thanks to a very knowledgeable and helpful former plant maintenance supervisor, this was done with remarkable efficiency. It did give us a good long look at the facility.
Age and inefficient layout are among the standard obsolescence factors in legacy plants of all kinds: manufacturing, extractives, or food processing. These obsolescence factors are most clearly seen in reduced production and profit. Originally built in 1947, the Sacramento food processing plant was the oldest in the Campbell’s system. Due to equipment age, inefficient facility layout, and the high cost to maintain the legacy equipment, the plant had also become the most expensive of Campbell’s plants to operate.
One example of Campbell’s legacy equipment is the original boiler facility, which was constructed in 1947. The boiler system and auxiliary systems required major equipment upgrades in 1990 and 2004.
You might wonder why some of this old, less productive equipment hadn’t been replaced. We explained in the appraisal report that the inefficient vertical plant design meant that maintaining, repairing or replacing the equipment had become a nightmare. The 4-story building, with food processing systems running from the top floor down – an efficient use of gravity to move product that remains in use only on the receiving end of some modern food processing plants – combined with narrow production areas and inadequate maneuvering space required wall removal to replace machinery. Imagine how that might delay production! Maintaining the Sacramento Campbell plant reportedly cost “millions of dollars per year,” considerably more than maintenance at other company plants in the network. The report discussed all of this in detail as part of the obsolescence factor determination.
In 2012, the Sacramento Business Journal wrote that the Campbell plant closure concluded a decades-long decline of food processing in the Sacramento region, which has at least a dozen former mills, canneries, fruit sheds, and packing plants scattered from downtown Sacramento to Roseville, Loomis and Newcastle.
Reading Comstock’s article reminded me of a great experience appraising the Campbell’s facility with Bob. It’s an honor to be a small – and mostly anonymous – part of Sacramento history.
Jack Young, ASA—MTS/ARM, CPA
Food Processing Equipment Appraisal & Appraisal Review
NorCal Valuation Inc.